Future-Ready with AI Inspections: Applying Computer Vision for Zero-Defect Manufacturing
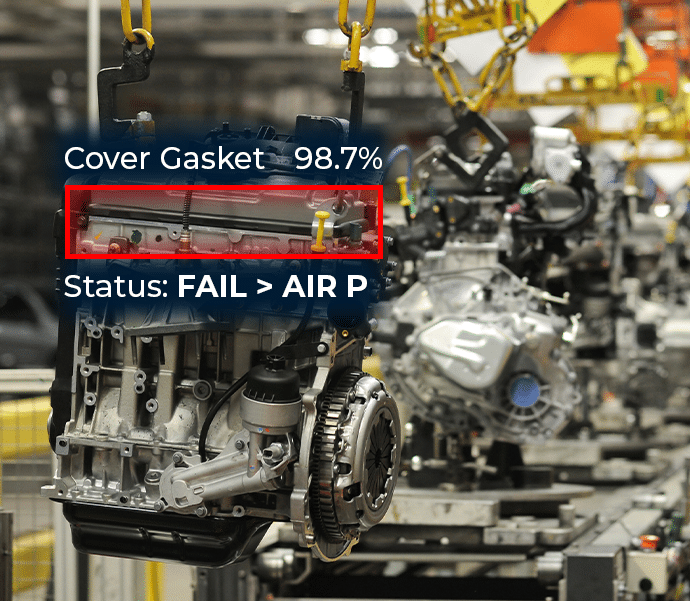
Matroid | April 15th, 2025
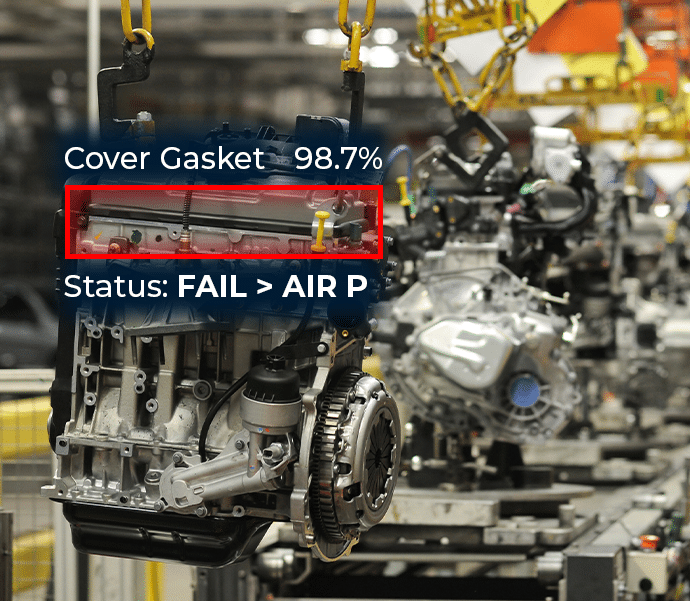
Every plant manager aspires to ensure that operations are safe, reliable, efficient, and compliant and that quality products come off the assembly line without defects.
Zero-defect manufacturing is a commitment to precision, a pivotal performance indicator for the world’s most critical industries. Identifying anomalies at the source before they become more significant issues that compromise production is vital to continually meeting market and consumer demands.
Autonomous detection using innovative technologies helps resolve inspection challenges by enabling accurate, data-driven insights to protect essential assets and prevent downtime. Industrial manufacturers leveraging AI-powered solutions with real-time analytics can maximize uptime while staying competitive with the latest technology.
Real-Time Monitoring for Factories of the Future
As manufacturers strive for flawless output, the absence of real-time defect detection could result in more costly repairs if product integrity issues go unnoticed. Traditional inspection methods for quality control can’t keep pace with the speed and complexity of modern production demands, making the shift to advanced technologies an imperative to lower risk and maintenance costs.
In the era of Industry 4.0, “factories of the future” are accelerating the use of automation to transform operational efficiency. Manufacturers have long understood the value of modernizing systems and processes to improve asset reliability and predictability.
Today’s industrial solutions increasingly rely on automation for error-free manufacturing, increasing safety while lowering costs. The next phase of digital transformation involves advancing artificial intelligence (AI) and machine learning (ML) tools for real-time continuous monitoring, which can pinpoint defects with greater accuracy and precision.
The advent of computer vision is a seismic shift in how manufacturing companies can increase visibility and quality control, keep operations on track, and stay ahead of compliance. By leveraging visual data and AI, companies can enhance asset reliability and maintenance programs, gain insights, and streamline production for consistently high-quality products.
As a next-generation visual inspection platform, Matroid Computer Vision activates real-time monitoring to spot defects before they become more significant problems. This helps manufacturers maintain consistent, zero-defect production.
The AI Technology Driving Zero Defects
Deep learning is a subset of AI and ML that uses algorithms inspired by the human brain’s structure and function, known as neural networks. These systems can discern subtle irregularities by processing vast images and video streams, significantly enhancing defect detection and reducing errors.
AI-based systems improve over time by continuously learning from new data, becoming more accurate and adaptable to changing conditions. This ongoing learning enables manufacturers to make quick, informed decisions in dynamic environments. Unlike rules-based systems that rely on static rules, deep learning systems evolve to tackle complex, ever-changing challenges with greater flexibility, precision, and reliability.ing them better tools.
Did You Know? Matroid applies AI/ML technologies such as deep learning to detect anomalies and perform tailored post-processing of visual data. These systems automatically recognize patterns and features from raw image data, learning from large datasets to quickly detect defects that rules-based systems might miss.
Redefining Inspection with Actionable Insights:
Computer Vision for manufacturing offers automated quality control that inspects, tracks, and alerts plant managers when production issues occur. Substantial gains in efficiency include:
- Anomaly Detection and Quality Assurance:
Quickly spot product defects and catch any deviations from standard procedures. This means taking immediate corrective actions and predicting maintenance needs to reduce the risk of nonproductive time. - Efficiency Optimization and Real-Time Monitoring:
Analyze production line footage to identify bottlenecks and deliver real-time feedback on quality. This helps operational teams optimize processes and swiftly tackle production issues as they occur.
Enhanced Reporting and Training:
Create automated reports and visual dashboards that highlight key findings. These insights help managers prioritize employee training needs and standardize processes across shifts for optimal and continual improvement.
The Next Level of Insight: PLC/MES Integration in Action
Building on these advanced AI capabilities, integrating Programmable Logic Controllers (PLCs) and Manufacturing Execution Systems (MES) takes operational efficiency to the next level. This integration bridges the gap between machinery and software, enabling seamless communication and real-time data sharing.
Unlike traditional systems, PLC/MES integration allows insights from production processes to be immediately actionable, driving faster responses and improved outcomes.
For example, when a defect, such as a misaligned component, is detected on the production line, the integrated system doesn’t simply analyze and identify the issue. The MES translates this insight into a specific corrective action, automatically triggering the PLC to adjust the machinery or alerting operators to intervene. This closed-loop feedback system reduces downtime and minimizes production waste.
Key Benefits:
- Faster Responses: Real-time data enables immediate action, reducing delays and downtime.
- Improved Product Quality: Continuous monitoring and analysis drive ongoing process refinement.
- Operational Precision: Keeps operations aligned with best practices, ensuring even better performance at scale.
PLC/MES integration streamlines production for more agile, responsive, and efficient inspection and predictive maintenance, resulting in smoother operations and manufactured products that meet — or even exceed — rigorous quality standards.
How to Maximize the Power of Visual Data
Manufacturers know that visual data is beneficial in analyzing processes, monitoring operations, and facilitating informed decision-making. Matroid Computer Vision transforms production lines across various industries with its automated visual inspection systems, enabling manufacturers to detect defects, streamline quality assurance processes, and operate efficiently without constant human oversight.
In steel manufacturing, computer vision identifies transverse and longitudinal cracks on slabs, providing 24/7 inspection with high precision and recall rates. In the automotive industry, computer vision is applied to inspect trim installations, detect missing underbody bolts, and ensure component accuracy while processing up to 60 vehicles per hour. Roofing manufacturers benefit from the technology’s ability to detect asphalt blobs and laminate leaks on shingles at speeds of 1,000 feet per minute, in addition to overcoming challenges such as varying colors and dusty environments.
Matroid Computer Vision identifies defects like cracks and rough edges on bricks while handling shape and pose variations in material production. It detects speed tears in extrusion profiles for aluminum manufacturers, accommodating diverse shapes and configurations with exceptional accuracy. As an effective detection solution for metalworking environments, it empowers manufacturers to maintain high-quality standards, reduce waste, and enhance operational efficiency while seamlessly integrating into their existing workflows.
By leveraging a diverse range of media — including images and video streams — computer vision captures intricate details of the production process. This capability allows manufacturers to monitor operations closely, make on-the-fly adjustments, and optimize efficiency to reduce downtime and ensure the highest quality standards.
With Matroid’s advanced computer vision technology, visual data becomes a goldmine of insights, turning raw images into precise, actionable feedback that helps manufacturers achieve zero-defect manufacturing across heavy industries such as automotive, aerospace, and steel production.
The Matroid Difference
- Historical and Predictive Analyses: Supports manufacturers in spotting trends, rapidly understanding common issues, learning from past mistakes, and enhancing decision-making with actionable insights.
- Real-Time Monitoring: Serves as an early warning system, alerting teams to potential issues before they escalate and enabling swift adjustments to optimize operations and maximize uptime.
- Empowering Manufacturers: Increasing visibility and control drives significant safety, reliability, and efficiency improvements while striving to achieve the highest caliber of performance across operations.
See the Future: Get the Matroid Demo
Advancements in visual inspection data and AI technology are redefining the future of manufacturing. As these innovations evolve, manufacturers should leverage all resources to drive quality and efficiency, paving the way for zero-defect production.
Data-driven decision-making gives high-performance industries a competitive advantage. It facilitates rapid responses and corrective actions to solve the most pressing operational challenges.
Ready to take the next step? Schedule a Matroid demo today to see firsthand how automating inspections can transform manufacturing processes with immediate ROI.
Download Our Free
Step By Step Guide
Building Custom Computer Vision Models with Matroid
Dive into the world of personalized computer vision models with Matroid's comprehensive guide – click to download today