Automated Defect Detection in Wind Turbines with Computer Vision
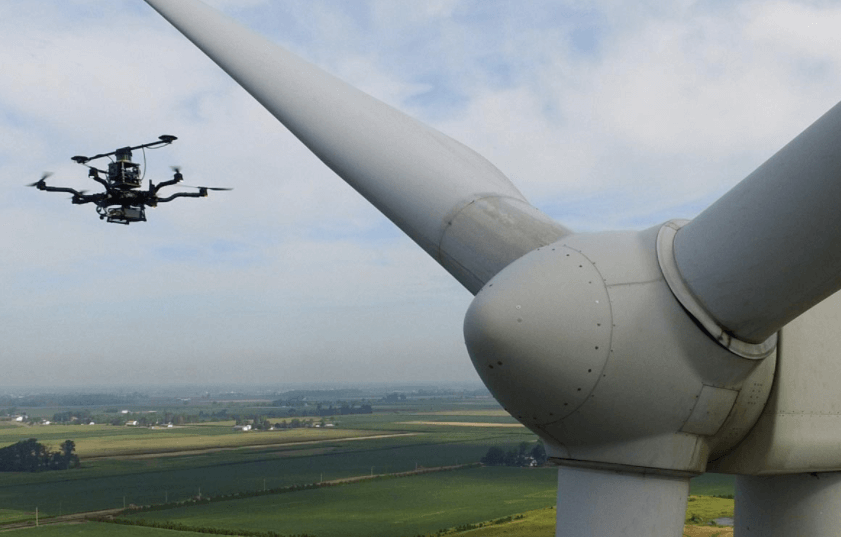
Chase Hart | October 19th, 2020
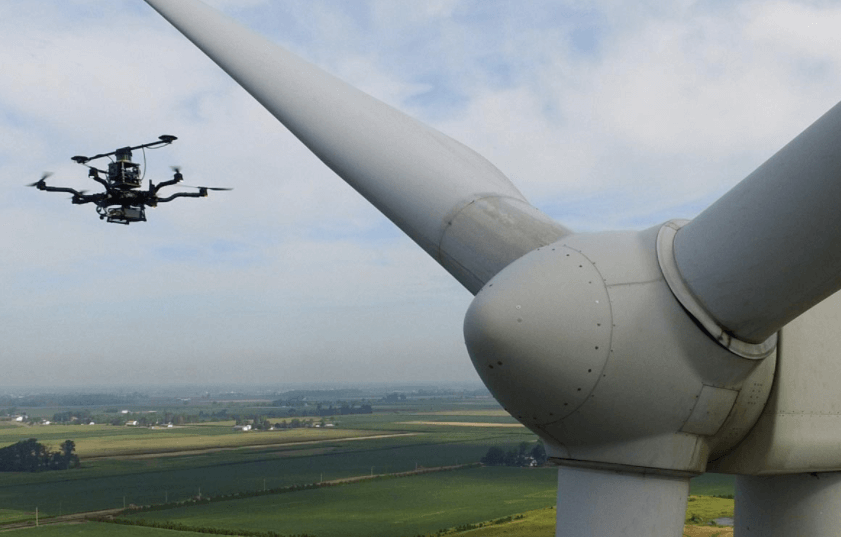
Wind power is one the world’s fastest growing sources of renewable energy. Generated by hundreds of thousands of wind turbines worldwide, wind energy is making the way we power the planet cleaner and more sustainable. However, wind turbines, like other power generating systems, are subject to normal wear and tear, as well as damage from numerous sources like lightning, hail, and rain. Left unchecked, they can fail unexpectedly, leading to significant financial loss and disastrous consequences.
To prevent this, wind turbines need to be inspected and maintained on a regular basis, which introduces significant costs in terms of both manual inspection time and money. Wind turbines are also often located on remote, rough, and sometimes even offshore terrain, which makes manual inspection dangerous. Even with the help of technologies like drones, a two-person inspection team composed of a drone pilot and a wind turbines technician can only inspect 12 turbines per day, at a cost of $800 per turbine. This not only limits the frequency of inspections, but also introduces inconsistencies and inaccuracies due to manual visual inspection.
Matroid solution: Automated defect detection
Automated inspection can be performed with a Matroid detector, an “automated pair of eyes” that leverages state-of-the-art computer vision to find objects of interest in visual media.
Using Matroid’s Studio, you can train detectors with practically any dataset. For this project, we took a drone inspection image dataset, cropped the images into smaller and more manageable patches, and uploaded them into Matroid Studio. After the images were uploaded, we annotated every anomaly in the images and then trained the detector with the press of a button. Within a few hours, we had a detector that takes in drone inspection images and automatically detects turbine damage. With just a couple days of work we had an accurate wind turbine defect detector that would have otherwise taken weeks or months to train from scratch.
On a held out test dataset of image patches, the detector performed well and was able to catch a majority of defects. During a real-world drone inspection, a video consisting of numerous images of the same blade of a wind turbine would be taken, which would further improving the discovery rate of defects. An inspector would then only need to manually inspect these detections instead of the full set of original images, significantly reducing the amount of manual work by a factor of 5 to 6, without compromising the quality and thoroughness of the inspections.
Importing and labeling training images in Matroid Studio is simple and fast with a few clicks
The detector is able to perform quite well on the test images
Matroid solution: Tracking defects with Collection Search
Beyond creating the initial detector with the Matroid Studio, Matroid can also help manage turbine inspection data with Similarity Search, a feature that enables millisecond level visual similarity search across archived or live media at scale. This is particularly useful for tracking minor defects over time to see how they have progressed and make estimates on when maintenance might be required. It can also be used to search for similar damages on other turbines, in order to get a sense of which types of issues are most common.
For example, in the below image, one can see that the feature is able to track the exact same damage in different pictures in the collection, taken at different times.
In another example, we use it for tracking the same kind of damage (scratches) in different places, showing us how certain damages can happen to multiple turbines in different locations.
Matroid solution: Real time detections for better and faster inspections
Matroid can also help monitor wind turbines in real-time with Stream Monitoring. With Stream Monitoring, you can connect your ONVIF compatibile cameras, monitor them with your detectors, and set up API and email based alerting for when objects or defects of interest are detected. For example, a drone pilot could use recent Stream Monitoring damage detections to choose which turbines to inspect further, conserving time and eliminating the need for having a wind turbine technician onsite closely monitoring the inspection.
Wind turbines are one of many examples of Matroid helping automate visual asset inspection in manufacturing and industrial IoT, improving asset longevity and productivity, whilst minimizing maintenance costs. To learn more about how Matroid could help you, get in touch with us today.
Download Our Free
Step By Step Guide
Building Custom Computer Vision Models with Matroid
Dive into the world of personalized computer vision models with Matroid's comprehensive guide – click to download today