Automated Steel Slab Defect Detection with Matroid Computer Vision: Achieving over 1900% ROI for a Large Steel Producer
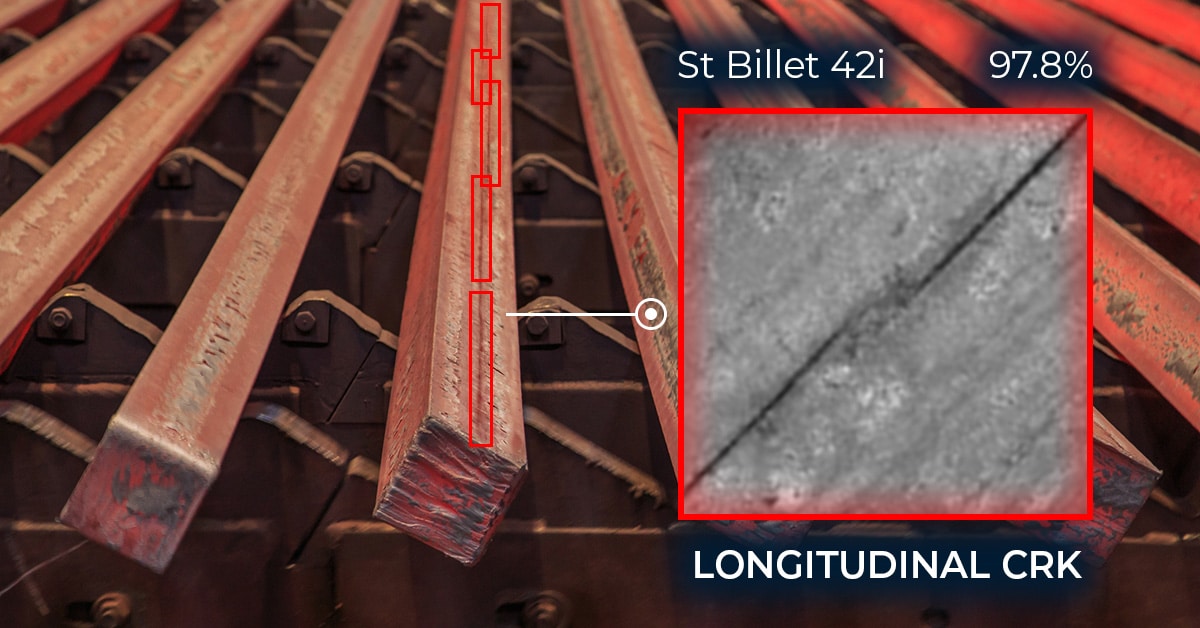
February 5th, 2025
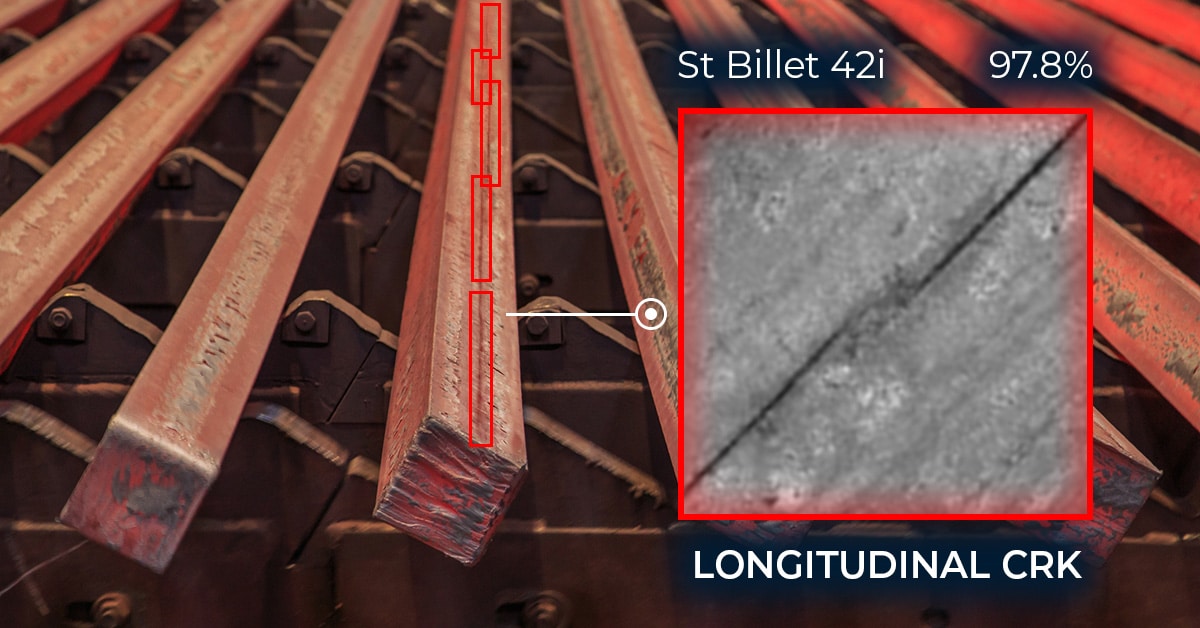
Problem
One of the USA’s largest steel producers faced difficulty detecting defects on steel slabs. Relying on human inspection has traditionally been an inefficient use of metallurgists and operators, consuming valuable time and effort that could be better spent on innovation and process optimization
On average, trained operators detected transverse and longitudinal cracks with only 60-70% accuracy throughout a full shift, highlighting the need for improvement. These cracks have historically been challenging to identify, requiring operators to visually inspect moving steel slabs directly from the caster while exposed to ∓900℃ temperatures.
To maintain operational efficiency and ensure higher quality control, the company required an automated system capable of identifying and classifying defects more accurately than human operators without slowing down production flow.
Solution
To tackle the challenge, Matroid partnered with the manufacturer to develop a cutting-edge computer vision detector. They combined the power of Matroid’s CV software with the expertise of on-site metallurgists. Together, they built and trained a highly performant detector that not only replicated the way operators identified defects but also surpassed the accuracy of the best human inspectors within days.
The detector was specifically trained to identify two primary types of surface defects, enhancing efficiency and precision in quality control:
- Transverse Cracks: Short, faint, horizontal cracks often appearing in vertical stacks.
- Longitudinal Cracks: Isolated, thin, vertical cracks of varying lengths.
Implementing Matroid’s computer vision technology improved detection accuracy from 60-70% to over 98% across all upstream inspections.
Results
By automating defect detection, the system significantly reduced the time metallurgists spent on routine quality control, allowing them to focus on upstream improvements and process innovations. This shift dramatically enhanced operational efficiency and resulted in substantial cost savings for the company.
Cost Savings: By automating defect detection, the company significantly reduced the risk of approving defective slabs, minimizing rework, material waste, and quality issues. This not only streamlined manufacturing but also lowered labor costs.
Previously, with 24/7 production, traditional inspection methods required multiple metallurgists on-site to manually inspect each slab. Now, a single Matroid license covers multiple sites and production lines, eliminating the need for tedious manual inspection and freeing up over a dozen metallurgists. These experts are now focused on production innovation and process improvements, driving long-term value in the caster process and saving the manufacturer over $2 million annually in redirected labor costs.
Enhanced Accuracy and Efficiency: By leveraging highly accurate computer vision detectors, the system significantly improved defect detection accuracy from 60% with human inspection to over 98% with Matroid. It outperformed trained metallurgists in identifying both transverse and longitudinal cracks, eliminating the need for manual inspection. This led to a substantial reduction in inspection time and labor costs while ensuring strict quality control standards were consistently met.
Streamlined Process: Once the detectors were quantified to perform at a higher accuracy than the metallurgists, the detection system became an integral part of the foundry’s “brain”— integrated directly into the Caster Pulpit – where real-time decisions are made to optimize production. This enabled the plant to immediately act when cracks were detected upstream, preventing defective slabs from moving downstream and stopping subpar material from continuing through the casting process. As a result, costly rework is minimized, and the risk of shipping defective products to consumers is significantly reduced.
Conclusion
By implementing Matroid’s AI-enabled defect detection system, one of the USA’s largest steel producers successfully transformed its quality control process. The automated system has delivered unparalleled accuracy in identifying transverse and longitudinal cracks. The detector has a precision of 99.8% and recall of 98.8%, a dramatic increase over the human operators, who averaged 60-70% throughout an 8-hour shift. This deployment has eliminated the inefficiencies and inconsistencies of manual inspection.
Beyond enhancing defect detection, the solution has unlocked over $2 million in annual labor redirection savings. It allows metallurgists to shift their focus from routine inspections to metalworking innovation and process optimization, driving long-term advancements in continuous casting. Additionally, the system has delivered incalculable savings by capturing defects before they continue downstream, preventing costly reworks and, more importantly, eliminating the risk of defective products reaching customers.
This deployment highlights how AI-driven automation enhances accuracy and efficiency and delivers tangible financial and operational benefits, positioning the company for sustained success in a competitive industry.
Enhance Metal Manufacturing Quality with AI-Powered Computer Vision
Leverage the power of Computer Vision to revolutionize defect detection in metal manufacturing. With our AI-driven platform, we eliminate manual inspection errors, improve production efficiency, and reduce scrap rates. See the technology in action—connect with our experts to discuss your unique challenges and tailor the system to your specific requirements—all without the need for coding. Start optimizing your quality control process today!