Automated Speed Tear Detection with Matroid Computer Vision: How AI Inspection can Streamline Operations in Aluminum Extrusion
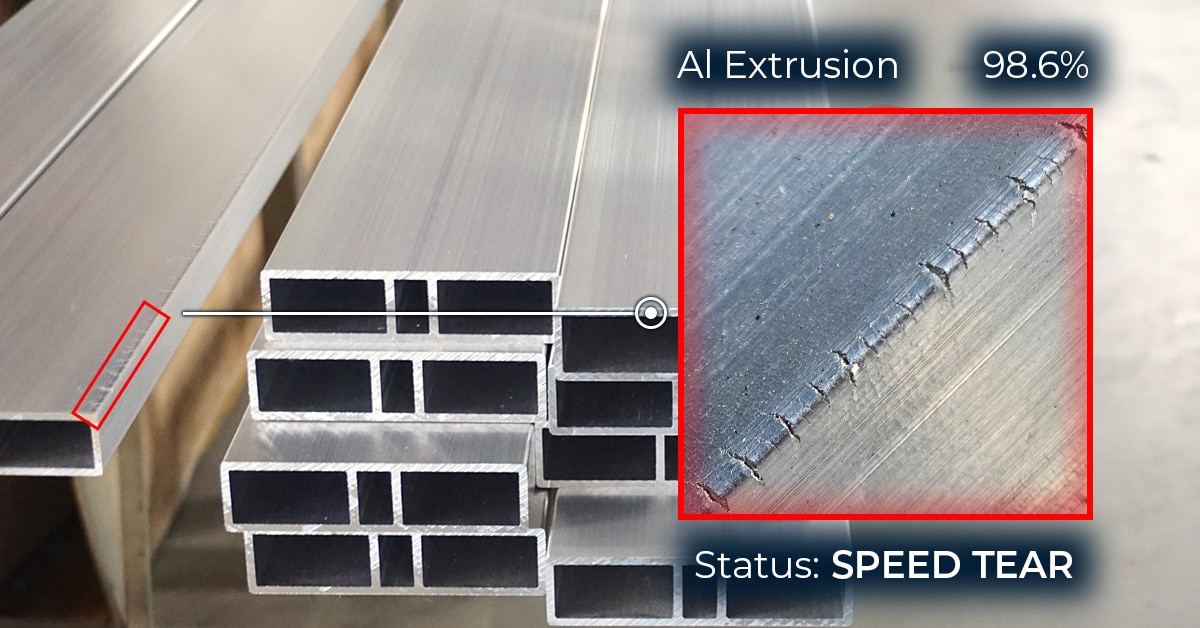
February 5th, 2025
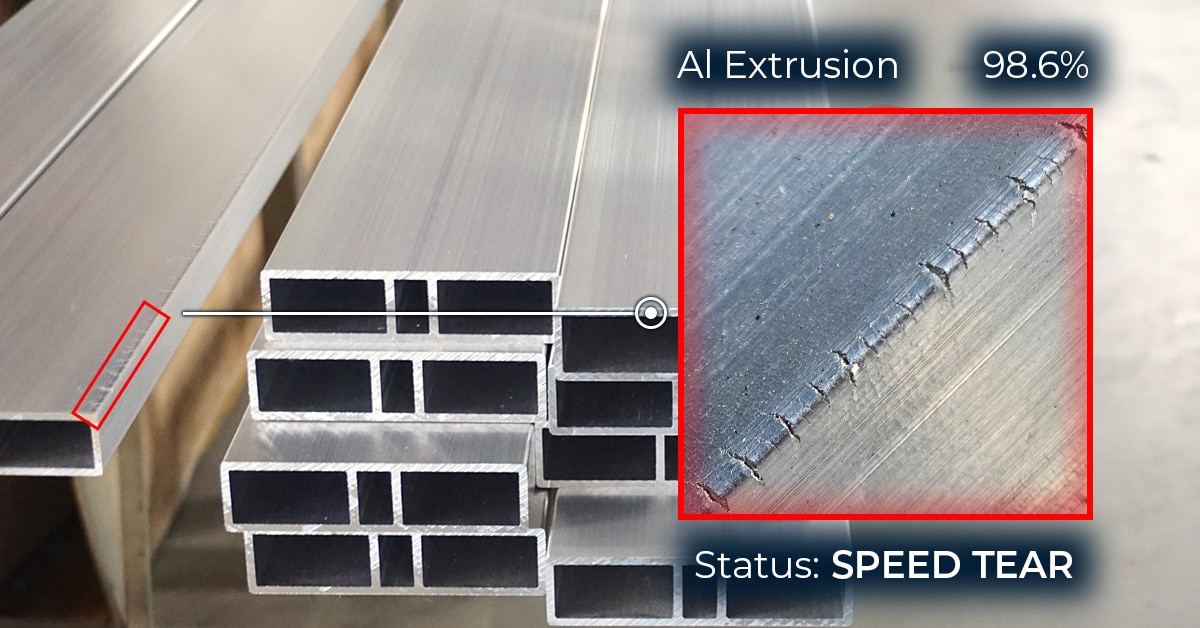
Overview
Quality control in aluminum extrusion is a complex, high-stakes process in which even the smallest defects can compromise product integrity. A global leader in aluminum extrusion partnered with Matroid to enhance its defect detection capabilities, seeking to eliminate human error and increase operator efficiency.
By replacing manual inspection with Matroid’s AI-powered computer vision system, the company significantly reduced missed speed tears, improved production speed, and ensured consistent quality inspection across all extrusion profiles.
Problem
The aluminum extruder invested excessive man-hours to prevent quality escapes in one of its high-value product lines. Speed and hot tears are process-driven defects that are often subtle yet highly consequential. If left undetected, they can catastrophically compromise the structural integrity of extruded aluminum products, making early detection critical. To maintain efficiency without sacrificing accuracy, the company required an automated system capable of detecting and classifying defects as effectively as human operators—if not better—without disrupting production flow. However, several key challenges stood in the way:
- Extrusion Profile Variability: The wide range of extrusion shapes and configurations made developing a universal detection system challenging. Some profiles also required internal inspections, forcing operators to examine several meters into the extrusion to identify tears.
- Specialized Lighting Requirements: Proper lighting was essential to enhance defect visibility and ensure accurate detection.
- False Positives: Differentiating true defects from normal process imperfections was difficult, as non-defect patterns often resembled actual defects. A robust annotation strategy was necessary to prevent misclassification.
- Visual Inspection Subjectivity: As the Process Engineering Manager noted, “You could ask five different people about a potential defect, and they each would have a different answer.” This inconsistency made standardizing defect identification challenging.
Solution
To address the issue, Matroid, and the Process Engineers worked together to build a computer vision detector that leveraged the power of Matroid’s computer vision software and the expertise of the operators on site. Together, they built and trained a highly performant detector that not only mimicked the way operators find defects but actually surpassed the accuracy of the best operators in a matter of days. The solution included:
- Optimized Lighting Techniques: Specialized illumination setups were implemented to enhance defect contrast.
- Capturing Operator Expertise: Matroid and the aluminum extruder collaborated to source various speed/ hot tear profiles. These were then clearly defined and labeled, creating a plant-wide standard for all packaging operators, metallurgists, and process engineers.
- Adaptive AI Detector: The system was trained on a diverse dataset encompassing various extrusion profiles, ensuring adaptability to different shapes and configurations.
- Smart Annotation Strategy: By distinguishing between real defects and non-defect patterns with the newly created “tear definitions,” the detector could quickly differentiate critical tears with minimal training data.
Results
With these innovations, the Matroid detector quickly outperformed packing line operators, achieving a higher defect capture rate within days. Its ability to accurately differentiate between genuine speed tears and misleading patterns significantly improved quality control, reducing waste and enhancing production efficiency. Additionally, by leveraging a well-balanced training approach, the detector eliminated the issue of subjectivity in defect identification, ensuring consistent tear classification and preventing slippage due to varied interpretations.
Once the Matroid detectors were validated to match or exceed operator performance, they were quickly integrated into the extruder’s operations. Now, operators receive real-time notifications if a batch contains tears, allowing them to reroute defective extrusions for rework or return before they continue downstream. This proactive approach frees up labor while preventing defective materials from being shipped—an especially critical improvement given the high-value nature of these extrusions, the intricate variations in extrusion profiles, and the expectations of end customers.
By implementing Matroid’s computer vision software, the aluminum extruder achieved standardized speed tear detection, significantly improving extrusion quality while reducing the need for manual inspection. This not only lowered associated costs but also freed up packing operators to focus on packing and loading products, ultimately accelerating production rather than diverting resources to search for defects.
Revolutionizing Metal Manufacturing with AI-Powered Defect Detection
Harness the power of Computer Vision to transform quality control in metal manufacturing. Our AI-driven platform automates defect detection, eliminating human error, reducing waste, and enhancing production efficiency. Experience the technology firsthand—connect with our experts to explore how AI can be tailored to your specific manufacturing needs, all without requiring coding. Take the next step toward smarter, more reliable quality assurance today!