How Quality Control Manufacturing Leverages Data for Smarter Processes
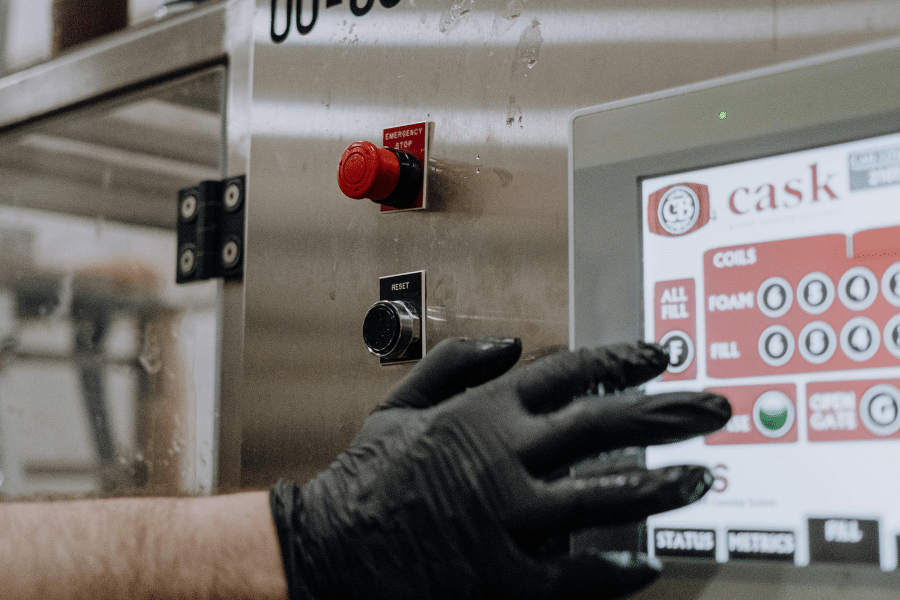
Jeff Zeller | January 29th, 2025
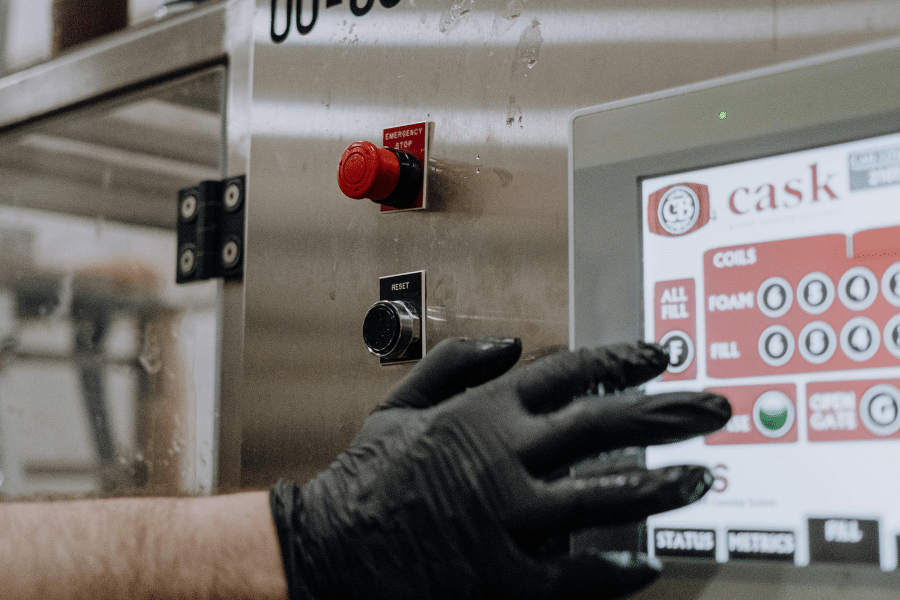
Today, data-driven technologies are for more than just analytics and decision-making. Manufacturers of all types of products are now using data to improve their quality control across the board. In this article, we’ll take a closer look at how the cutting-edge manufacturers of today are using data to simplify and streamline their quality control to result in better processes and products for everyone.
Quality Control: The Traditional Way
Before data-driven processes could be put into place on a large scale, manufacturers relied heavily on manual inspections and human judgement. Visual inspections to look for things like scratches, dents and misalignments were prone to human error and fatigue. Even manual measurements using tools like micrometers and calipers depended entirely on the speed and skill of the operator.
Other methods like sample testing and even using mechanical testing equipment were extremely limited which slowed down production. Although these methods were more thorough, they could only test specific attributes, which might mean that larger issues would be missed.
Quality Control Using Data-Driven Insights
Data-driven insights bring a variety of benefits to manufacturing processes, enabling companies to go far beyond surface defects and gauge quality at scale. This eliminates potential bottlenecks while providing a continuous feedback loop. Here’s how data-driven insights can help:
Real-Time Monitoring
Advanced sensors and IoT (Internet of Things) devices help manufacturers gather data in real-time from machinery, production lines and even the individual products themselves. These devices continuously track and report on different parameters including:
- Temperature
- Pressure
- Vibration
And more, flagging any deviations from the current standards. With this real-time data, manufacturers can get instant alerts when any issues are detected, as well as on-the-fly adjustments.
Visual Inspection Automation
Computer vision and machine learning technologies are changing visual inspection. With high-resolution cameras and detailed algorithms, images and videos of products can be quickly analyzed to see defects that ordinary human quality control can miss. This results in faster inspections compared to manual checks, as well as improved accuracy across the board.
Predictive Maintenance
Data from sensors can be used to predict possible equipment failures before they happen. By analyzing trends in vibration, noise or other metrics, predictive models can alert operators when maintenance may be needed. This in turn maximizes machine uptime while reducing unnecessary maintenance costs.
Data-Driven Decision Making
Through data-driven decision-making, manufacturers can collect and analyze a wide range of data from the production floor. This not only reveals possible mechanical issues in the production machines themselves, but also helps manufacturers spot:
- Potential defects
- Areas for workflow optimization
- Recurring issues that, once eliminated, result in better product designs
Improved Traceability
Data-driven systems also include detailed records of every step of the process, from raw items to the finished result. Having each step stored in the system offers improved traceability which is a must for regulatory compliance as well as taking steps to resolve and isolate defective batches.
Having a record of each step and any issues encountered also helps improve accountability across the entire supply chain in case of issues.
Adaptive Quality Control
One of the best reasons to upgrade to a data-driven equality control process is the exciting potential of AI and machine learning. These systems learn from the data and improve their processes accordingly.
For instance, AI algorithms can adjust tolerances dynamically based on different conditions. Quality thresholds can be fine-tuned to balance production speed with defect rates. These processes are something that would take considerable time and the need to overhaul the current system if they were implemented manually.
Integration with MES and ERP Systems
Data from quality control processes can be integrated with Manufacturing Execution Systems (MES) and Enterprise Resource Planning (ERP) systems. This gives managers and business owners a more complete view of operations. In this way, quality control can communicate seamlessly with other departments, which leads to better supply chain management and inventory along with centralized dashboards to support high-level decision-making.
Getting Started with Data-Driven Manufacturing Processes
It’s easy to get started with integrating data-driven processes into your existing manufacturing system. Not only will taking these steps minimize waste by making sure only the highest-quality products are manufactured, but they also empower the workforce to focus on more strategic tasks rather than manual inspections.
Detailed tools, like Matroid, are designed to deliver the latest in computer vision. With a powerful API and helpful quick-start documentation as well as templates and helpful support, there’s no faster way to start implementing this cutting-edge technology into your existing processes.
Matroid automates visual inspection while providing real-time monitoring and feedback. Through a combination of advanced computer vision and deep learning systems, Matroid helps manufacturing businesses large and small output the highest quality standards across all production systems.
At its core, Matroid’s anomaly detection lets the system analyze irregularities and defects that go well beyond surface scratches and dents. It can spot chips, cracks, discoloration, missing or incorrect assemblies with ease. Oftentimes, computerized visual anomaly detection ends up with algorithms that lack material or data that trains them on manufacturing systems.
This is precisely where Matroid excels, training their systems with unlabeled data and greatly shortcutting the learning process. Even as a manufacturing process changes over time, whether through equipment wear and tear, changes in raw material or new product designs, Matroid adjusts to these instances of “concept drift”, continuing to keep up with anomaly detection even as equipment is swapped out or other items change along the production path.
We invite you to learn more about how this powerful, cutting edge system can improve your company’s productivity while helping to spot and flag errors and improve the manufacturing process. Book a demo with one of our helpful computer vision experts or check out our blog to learn more about the leaps we’re making in AI-driven visual inspection. See for yourself how proven systems like Matroid can save time and money while improving quality and delivering data-backed certainty to your manufacturing business.
Download Our Free
Step By Step Guide
Building Custom Computer Vision Models with Matroid
Dive into the world of personalized computer vision models with Matroid's comprehensive guide – click to download today