Leveraging Computer Vision to Improve Efficiency, Quality Control, and Workplace Safety in Metal-Forming
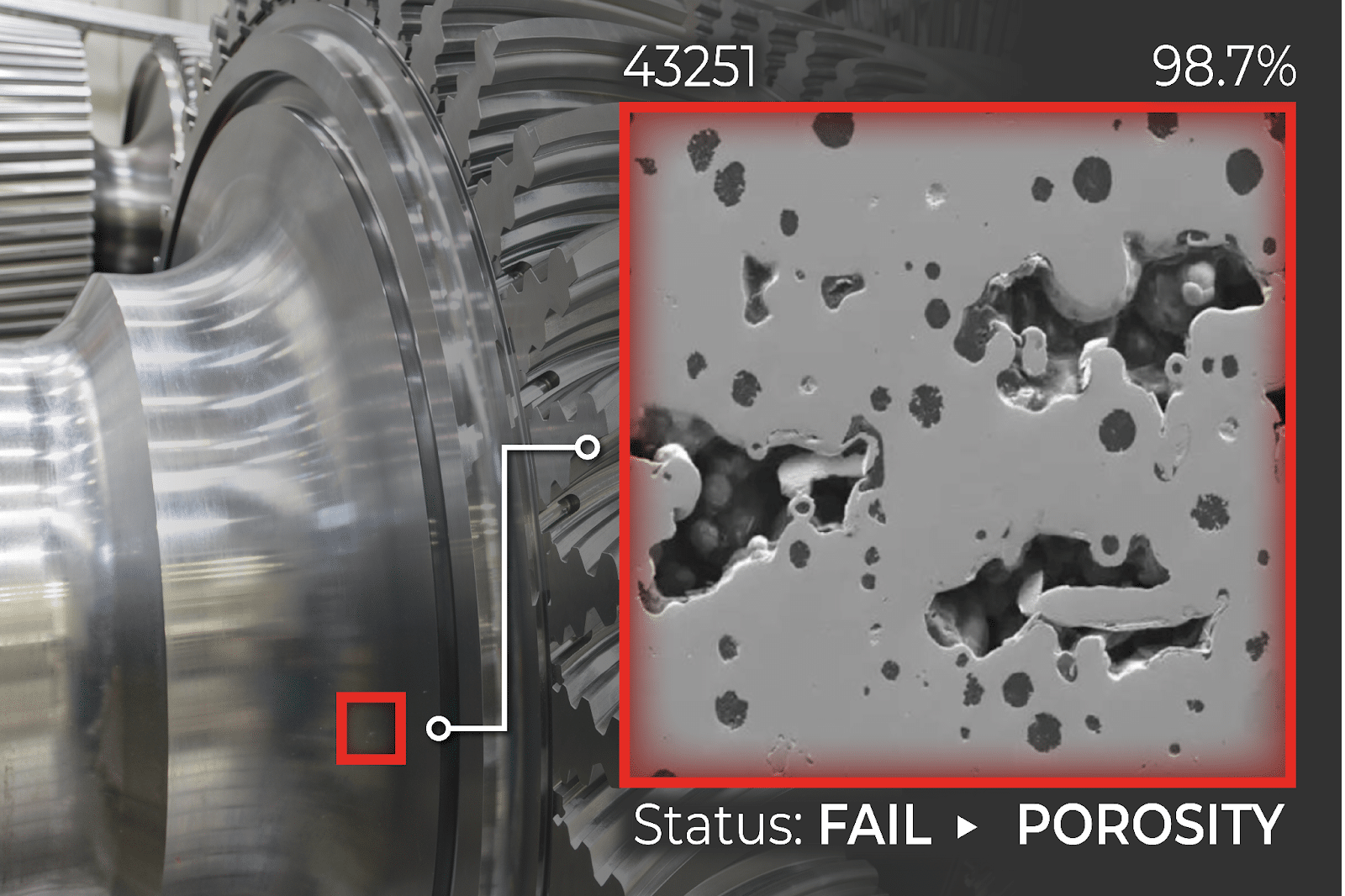
Matroid | June 14th, 2024
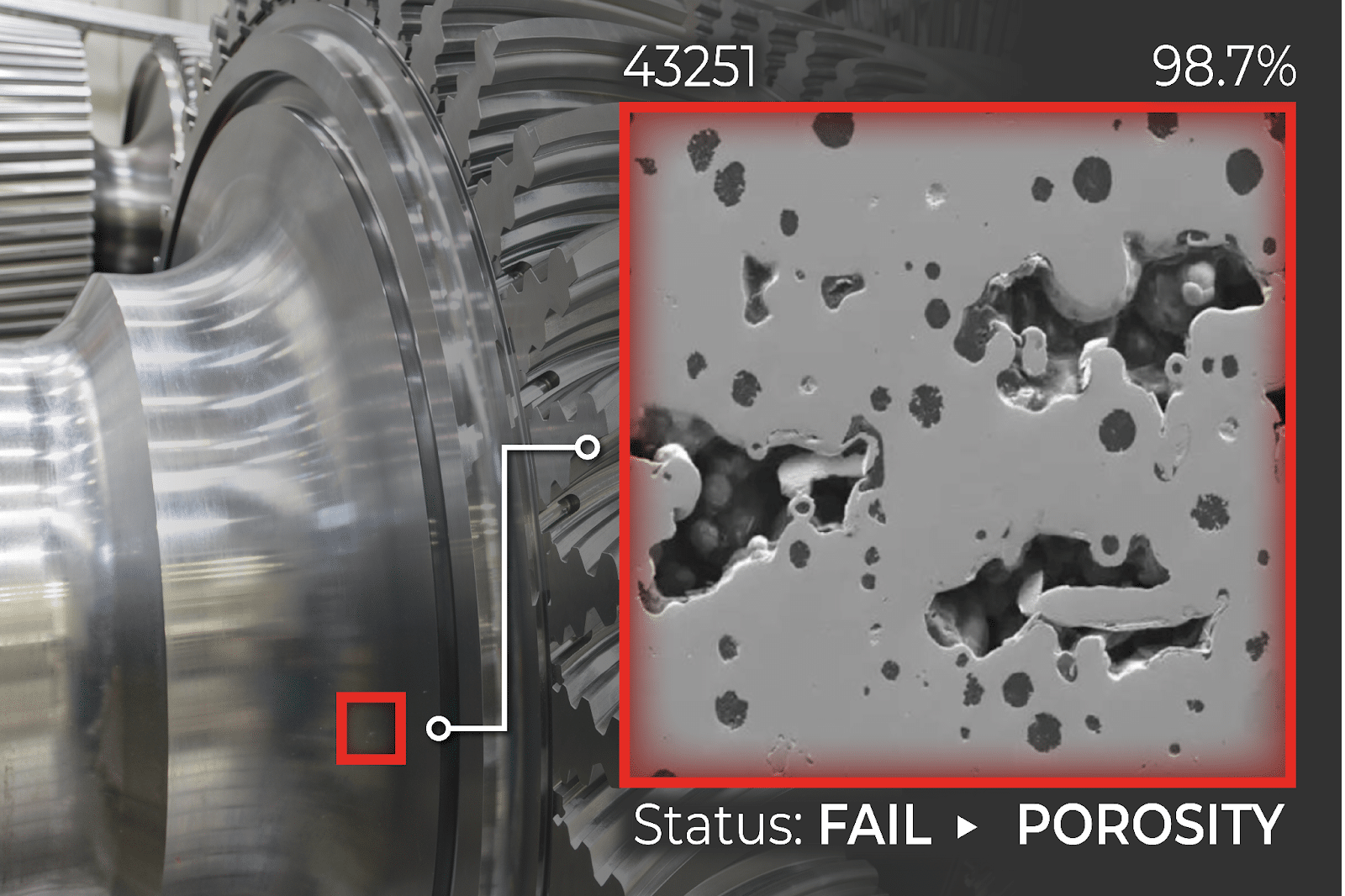
From detecting potential safety hazards to ensuring compliance with industry regulations, computer vision offers a comprehensive toolkit for enhancing operational processes and safeguarding workers.
In the metal forming industry the integration of computer vision (CV) technology is proving to play an instrumental role in transforming workplace operations and, notably, in enhancing ROI on production processes. The improvement of quality control efficiencies in turn have a significant and direct impact on strengthening workplace safety initiatives.
The Power of Computer Vision in Improving Metal-Forming Operations
In an industry where every aspect of production efficiency matters, the ability to improve both operations and safety through CV technology holds particular significance. By leveraging CV, metal formers can realize substantial cost savings across various facets of their operations.
Computer Vision Applications in Metal-Forming Operations:
- CV-enabled real-time monitoring and analysis of production processes can identify inefficiencies and bottlenecks, enabling timely adjustments to enhance productivity.
- CV systems can assist in predictive maintenance, identifying equipment issues before they escalate into costly breakdowns. This proactive approach to equipment maintenance not only reduces downtime but also extends the lifespan of machinery, resulting in long-term cost savings for metal forming companies.
- By streamlining workflow processes and optimizing resource allocation, computer vision technology can minimize waste and improve overall operational efficiency. This leads to increased throughput, reduced lead times, and ultimately, higher profitability for metal formers.
Moreover, the data insights generated by CV systems enable informed decision-making and process optimization. By analyzing data on production performance, resource utilization, and quality control metrics, metal formers can identify areas for improvement and implement targeted strategies to enhance efficiency further.
The Intersection of Efficiency and Safety
In addition to improving operations, such as the efficiency gains mentioned above, computer vision (CV) technology directly enhances workplace safety and productivity. More specifically, artificially intelligent visual inspections systems excel at anomaly detection by swiftly flagging irregularities in equipment operation or deviations from standard procedures. This ensures manufacturing processes remain within specified parameters, minimizing defects, optimizing product quality, and identifying potential safety hazards in real-time.
Matroid’s Computer Vision in Action
Adoption of Matroid’s computer vision platform across operations has significantly improved both operational efficiency and safety for Service Center Metals (SCM), an aluminum extrusion and billet manufacturing plant. The AI technology allows for precision monitoring and immediate corrective actions in day-to-day operations.
Examples include:
- In remelt furnace operations, Matroid’s AI enables precise monitoring of skimming and timing activities, reducing metal loss and identifying optimal operator practices. It corrects inaccuracies in manual metal charging, leading to more accurate inventory reports and reducing reliance on more expensive primary aluminum. The CV improves safety by mitigating risks such as molten metal explosions and unsafe operator practices.
- In aluminum extrusion operations, Matroid’s CV detects safety violations, such as the absence of gloves. The system provides instant alerts to supervisors, allowing for immediate corrective actions and increased safety awareness. CV can integrate automatic machine shutdowns when operators are in hazardous positions, safeguarding operator safety and refining safety management protocols.
- Matroid’s CV system, equipped with advanced object detection capabilities, can be used to proactively detect critical safety issues. Specifically, after partnering with Matroid, SCM boosted airbag compliance rates from below 25% to over 90% by analyzing recorded video from SCM’s shipping docks. Beyond airbag compliance, Matroid’s proactive detection improved overall safety by identifying risks associated with working at height during metal handling at SCM’s shipping and receiving docks. Read more about how Matroid’s AI Computer Vision (CV) technology emerged as a powerful force in reshaping workplace safety here.
Ultimately, the integration of computer vision into metal-forming operations has proven to streamline processes, improve quality control, strengthen safety measures, and improve environmental stewardship. Future innovations in safety and efficiency will only solidify CV’s role in operational strategy.
Seizing Opportunities with Computer Vision Technology
As optimism grows within the metal forming industry, computer vision (CV) technology emerges as an essential asset. Fabricator Magazine highlighted findings from a recent Precision Metalforming Association (PMA) Business Conditions Report, indicating a sustained improvement for the third consecutive month among metal forming manufacturers.
With heightened production demands anticipated, CV offers needed support in optimizing efficiency, ensuring quality, managing workforce dynamics, controlling inventory, and maintaining safety compliance. From real-time monitoring of production processes to automated visual inspections of manufactured parts, CV solutions are poised to assist metal formers in capitalizing on the positive momentum and sustaining long-term growth.
Why Matroid?
Matroid’s no-code computer vision (CV) software empowers professionals at all skill levels to harness the power of artificial intelligence in visual inspection, and as a result, drive performance and accuracy in metal forming processes.
Using Matroid’s coding-free computer vision models:
- Detector development becomes a streamlined process.
- Engineers and supervisors can build custom detectors using annotated data and leverage the platform’s intuitive interface for quick iteration and refinement.
- Continuous improvement and enhanced quality control processes are achieved with automated detector versioning that enables easy comparison and tracking of detector performance over time.
Additionally, Matroid’s machine learning software seamlessly integrates with existing video/camera infrastructure and new installations, ensuring consistent CV implementation across safety and compliance protocols.
Unlock the Potential: Schedule Your CV Demo Today
CV technology holds immense potential to revolutionize various facets of metal forming operations, from real-time hazard detection to quality control and beyond. By integrating computer vision, companies can stay ahead of the curve, adapt to evolving industry demands, and maintain a competitive edge. See how Matroid’s CV can improve operations by scheduling a demo with us.
Download Our Free
Step By Step Guide
Building Custom Computer Vision Models with Matroid
Dive into the world of personalized computer vision models with Matroid's comprehensive guide – click to download today