The Role of Automated Visual Inspection in Modern Manufacturing
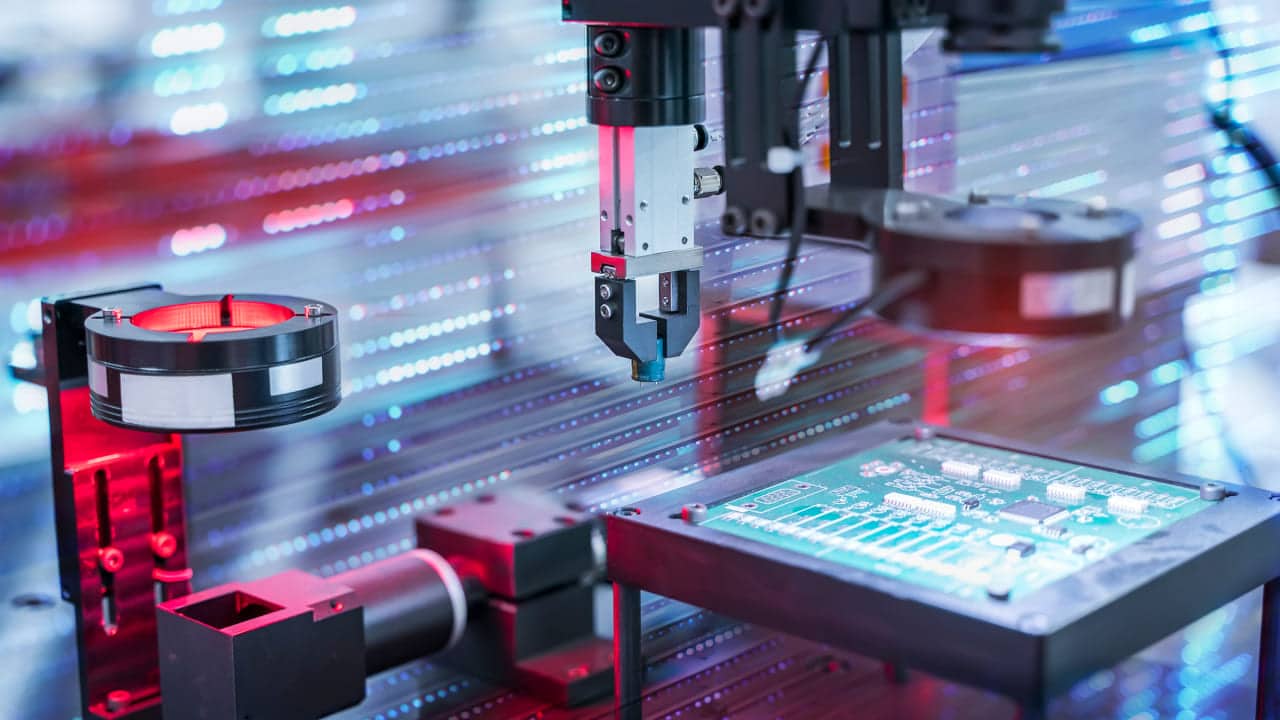
Matroid | October 30th, 2024
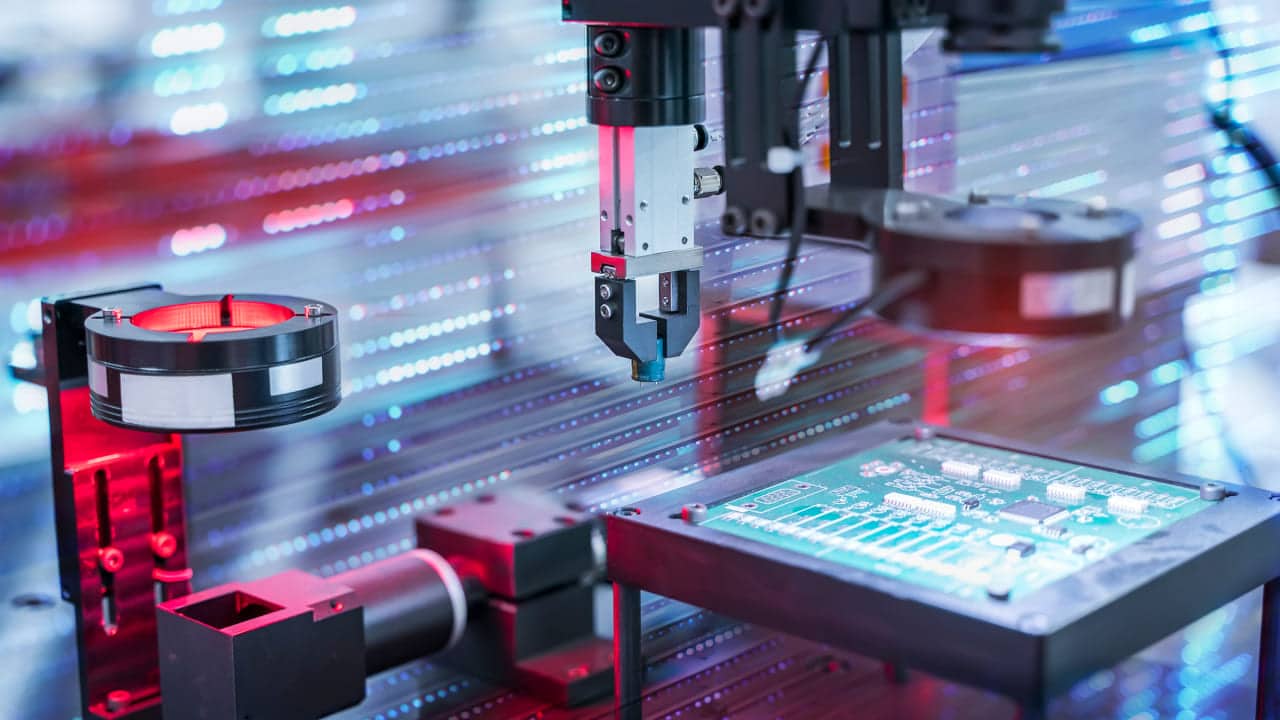
Maintaining high-quality standards is critical, especially with the global competition and consumer demand for flawless products. Manufacturers are under immense pressure to deliver excellence consistently. By implementing automated visual inspection systems (AVI), companies are revolutionizing quality control processes, ensuring precision and efficiency.
Understanding Automated Visual Inspection Systems
Automated Visual Inspection (AVI) systems are advanced quality control tools leveraging high-resolution cameras, sensors, and sophisticated algorithms to examine products for defects or deviations from specifications. Unlike manual inspection, AVI systems offer machine-based accuracy, detecting misalignments, size discrepancies, and surface defects that might escape the human eye.
Components of AVI Systems
AVI systems comprise essential hardware and software components that enable precise and reliable inspections. Key hardware components include high-resolution cameras for capturing detailed images, specialized lighting systems tailored to enhance specific features, and various sensors to detect abnormalities. On the software side, image processing applications analyze captured images, while machine learning algorithms enhance system accuracy by learning from past inspections. A user-friendly interface allows operators to control the inspection process seamlessly.
The Evolution of Inspection Technology
Inspection technology has evolved significantly, transitioning from manual to automated methods. Initially, quality control relied on human inspectors, prone to fatigue and errors. Early automation introduced basic image capture but was limited in adaptability. Integrating advanced computer vision and AI has revolutionized the field, allowing systems to learn and adapt without explicit reprogramming and enhancing precision.
Benefits of Automated Visual Inspection in Manufacturing
Automated Visual Inspection systems bring many benefits to manufacturing, enhancing quality assurance, increasing efficiency, reducing costs, and providing scalability and adaptability.
Enhanced Quality Assurance
AVI systems significantly improve defect detection accuracy, resulting in fewer faulty products reaching consumers. AVI systems use high-resolution cameras and AI algorithms to detect surface defects, assembly errors, and component misalignments with unprecedented precision. Real-time monitoring provides immediate feedback, enabling rapid adjustments to maintain rigorous quality standards.
Increased Efficiency and Productivity
AVI systems inspect products at speeds beyond human capability, enhancing productivity and efficiency without compromising quality. With minimal human intervention, these systems streamline operations through continuous 24/7 operation and automated decision-making based on predefined criteria.
Cost Reduction
Early defect detection minimizes waste and rework while reducing manual inspection costs. AVI systems contribute to significant labor cost savings by reallocating human resources to more complex tasks.
Scalability and Adaptability
AVI systems offer scalable solutions for diverse manufacturing environments, with easy deployment and the flexibility to adapt to new inspection criteria. Matroid’s no-code platform exemplifies this adaptability, enabling manufacturers to respond rapidly to changing standards and product evolutions.
Applications of Automated Visual Inspection in Manufacturing
AVI systems have versatile applications across various manufacturing sectors and are crucial in defect detection, process optimization, and workflow verification.
Defect Detection and Quality Control
AVI systems excel at identifying surface defects, assembly errors, and component misalignments, ensuring product conformity and adherence to specifications. Currently, Matroid is collaborating with a leading automotive manufacturer to address issues such as alignment irregularities in vehicle bodies, contributing to enhanced safety and quality control. Automotive manufacturers use AVI to inspect car bodies for paint defects and component alignment, while electronics manufacturers check circuit boards for solder joint defects and placement errors.
Process Optimization
By providing insights into production processes, AVI systems facilitate continuous improvement. Data analysis helps identify recurring issues, track process stability, and optimize production parameters. Automated inspection tasks enhance throughout, demonstrating significant improvements in production efficiency.
Future Trends and Innovations in Automated Visual Inspection
Technological advancements continue to shape the future of AVI systems, integrating with cutting-edge technologies like AI, IoT, and robotics to enhance capabilities and impact.
Advanced AI and Machine Learning
Integrating sophisticated AI and machine learning algorithms revolutionizes AVI, enabling deep learning for complex pattern recognition and transfer learning for rapid adaptation to new products. Explainable AI provides clear reasoning for decisions, which is important for regulatory compliance and process improvement.
Integration with IoT and Robotics
The fusion of AVI with IoT creates connected manufacturing environments, allowing real-time data sharing and predictive maintenance. Robotics enhance flexibility, with mobile inspection units and cobots handling repetitive tasks, complementing human inspectors in complex decision-making.
Edge Computing and Smart Manufacturing
Edge computing brings processing power closer to inspection points, reducing latency for real-time decisions and addressing data security concerns. AVI systems play a central role in smart manufacturing, enabling lights-out operations, mass customization, and sustainability efforts by minimizing waste and supporting life cycle monitoring.
Matroid’s Unique Value in Automated Visual Inspection
Matroid’s no-code, AI-driven visual inspection solutions provide unmatched ease of integration, scalability, and a user-friendly interface, transforming manufacturing processes with enhanced precision, reduced defects, and improved operational efficiency. A significant differentiator is Matroid’s camera-agnostic platform, which can leverage any type of visual sensor. Unlike other AVI systems that require highly specialized vision equipment, Matroid can utilize any image-producing device to detect defects, making it versatile and adaptable to a wide range of inspection needs. This flexibility allows non-programmers to deploy sophisticated inspection models quickly, streamlining implementation and adaptation to evolving industry standards.
Conclusion
Automated Visual Inspection systems are transforming quality control in modern manufacturing, offering unparalleled accuracy, efficiency, and consistency. By leveraging AI and machine learning, AVI systems enhance defect detection and process optimization, playing an essential role in maintaining competitive advantage. Manufacturers are encouraged to explore AVI solutions, such as Matroid’s platform, to elevate their quality control processes and stay at the forefront of industry innovation.
Are you prepared to elevate your manufacturing capabilities to unprecedented levels? Request a demo of Matroid’s cutting-edge visual inspection solutions today. Discover firsthand how you can drive transformative improvements in precision, quality assurance, and operational efficiency. Partner with us to spearhead a new era of innovation and bolster your company’s competitive edge.
Download Our Free
Step By Step Guide
Building Custom Computer Vision Models with Matroid
Dive into the world of personalized computer vision models with Matroid's comprehensive guide – click to download today